2022 News
Bringing Advanced Technology to a Nearly Century-Old Operation
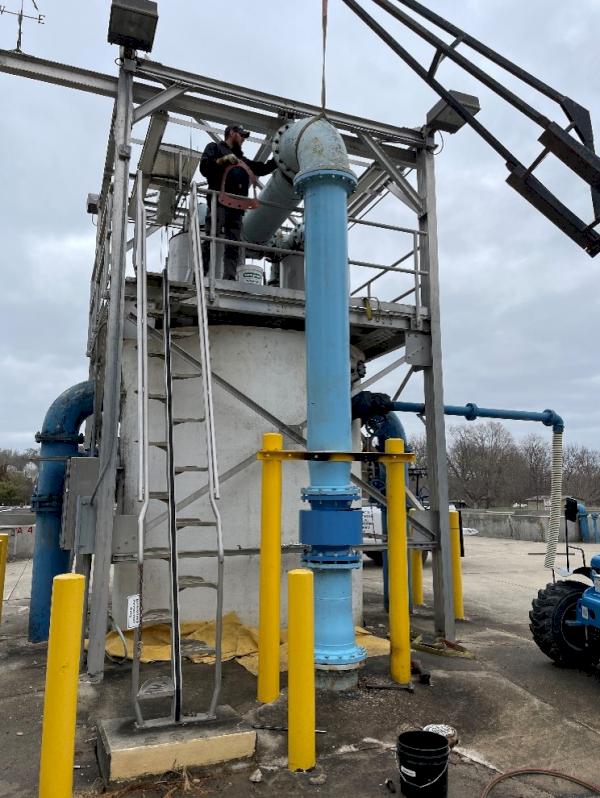
Tucked up in Northeast Iowa, the Chuck Gipp Decorah Fish Hatchery raises more than 100,000 catchable-size rainbow trout annually to stock waterways throughout the state. The all-day, every-day operation turned to Baker Group for a recent upgrade that has brought greater efficiency and ease-of-use to its automation systems.
Built in the 1930s as a project of the Civilian Conservation Corps, the hatchery is a state-managed operation with an iconic look including a stunning limestone office and residence. The hatchery itself has 24 cement flow-through raceways and three rubber lined earthen ponds. The team at the hatchery is responsible for stocking a total of 15 put-and-take streams in Allamakee, Howard, Mitchell and Winneshiek counties. Additionally, the hatchery stocks seasonal urban lakes in Mason City, Sioux City, Spencer, Ames, Ankeny and Bondurant.
The hatchery needed a major upgrade to systems that monitor everything from waterflow and ambient temperature to several measures related to fish health. Because of the complexity of the project, the necessity that systems remain active throughout the project, and the requirement the contractor has certification in the installation and maintenance of Phoenix Contact Systems, the retrofit required the vast expertise a company like Baker Group possesses.
“It was a big job,” says Project Manager Mike Pedersen, who works from Baker Group’s Quad Cities office. “We were confident we would be successful with this project because we have the technical skill to design a system to replace what they were using, and we also have a good deal of experience working closely with the state.”
After participating in a competitive bid process, Baker Group was awarded the project in October 2021. The first step was planning the project.
“This required we work with state timelines, so we spent a good amount of time early on doing our engineering design work and electrical planning,” Pedersen says. “This also required we put a plan together that would allow us to use temporary controls when we removed the old and installed the new. This was a situation where we couldn’t just shut the whole operation down to complete the project.”
The project revolved around installing PLCnext Technology — essentially an advanced Internet of Things (IoT) solution — to replace all the legacy controls and measurement devices in the hatchery. PLCnext Technology enables the build of an ecosystem for industrial automation and consists of open hardware, modular engineering software and easy-to-access digital software that allows for precisely tailored design of automation systems.
While Pedersen and the Baker Group team were comfortable with the technology, the logistics of the job presented a challenge.
“The hatchery is a 24-hour-a-day, seven-day-a-week, 365-day-a-year operation that requires constant monitoring of the fish and their environment to ensure they survive,” Pedersen says. “The main challenges we faced were maintaining waterflow and electricity on all systems for the duration of the project. There was also some complex mechanical work that needed to be performed as well.”
It was the multiple complexities that made Baker Group perfect for the job.
“Most companies who are good at automation don’t do complex mechanical work,” Pedersen says. “We were able to leverage our company-wide skill set and multiple business units to ensure this project was a success from start to finish.”
The most pressing challenge was that documentation or schematics of the existing system were not available. The entire system had to be traced out by hand and electrical schematics were derived from walkdown notes. Adding to the complexity was the fact that no wiring was labeled and it often changed color multiple times inside the existing conduit.
And that’s not all. It was critical the existing alarm autodial system be maintained and the team at Baker Group could design and implement an interface to allow the new PLC system to talk to the archaic autodialer. The specific and unique challenge of the job required months of planning and design.
The resources dedicated to preparation, planning and design proved vital in ensuring the actual upgrade could be completed in just days. During the project, each of the aforementioned challenges were addressed and a temporary solution was installed to run necessary systems while the switchover to the new platform was installed. The project was completed in two phases:
- In Phase 1, the Baker Group team performed all 16-inch piping modifications and 14-inch flow meter installation.
- In Phase 2, the Baker Group team demolished the entire hard-wired system and installed new PLCnext Technology automation components.
“We moved in a logical path around systems,” Pedersen says. “For instance, we would take the system that ran the aeration pumps down for a few minutes to install the new automation. As soon as the new system was up, we would test it. When we were sure it was working correctly, we would move on to the next system.”
The time and resources spent planning paid off and ensured the project went off without a hitch. When completed, the new PLCnext Technology replaced a system that had been in use since the facility opened nearly 100 years ago.
“The way the fish hatchery was controlled was through hand automation and a relay kind of logic,” Pedersen says. “It was all hand wired, very old and not run on or through a computer. We were able to bring it up to the 21st century with the ability to run systems and access data in real time from virtually anywhere.”
The added benefit of an automated system leveraging the PLCnext Technology is that it allows for more efficient storage of historical data. Instead of having to keep paper logs of key measures, the new system builds a database automatically that allows the team at the hatchery to see detailed trends on things like pH levels, historical temperatures and more.
The Automation Unit led the project with key contributions from the Industrial Unit and Mechanical Unit. Pedersen says this was Baker Group’s first fish hatchery job and it fit nicely with the company’s “we can do that” approach.
“The automation aspect of the job was pretty common,” he says. “The difficult part was some of the pipe work that needed to be done and using the PLCnext platform. But honestly, these are the kinds of challenges we thrive on at Baker Group. We are willing to take on the job because we know we have the expertise as an organization to get it done.
“This one was especially satisfying. Being able to participate in a project that literally took a system that had been in place for nearly a century and upgrading it with a technological solution like we did was exciting to be a part of.”
About Baker Group
Baker Group is a commercial and industrial specialty contractor based in Ankeny, Iowa. With more than 1,100 employees, Baker Group is the Midwest’s premier full-service specialty contractor providing mechanical, industrial, sheet metal, electrical, building automation, process automation, security systems, fire alarm systems, parking/revenue controls and 24/7/365 service. For more information, call 855.262.4000 or visit www.thebakergroup.com.
News
Best of Des Moines 2024
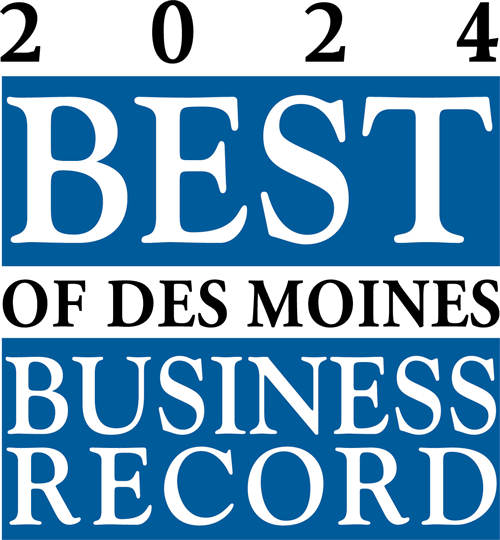
Baker Group was recognized by readers of the Des Moines Business Record for Des Moines' Best Mechanical Contractor for the 18th consecutive year.